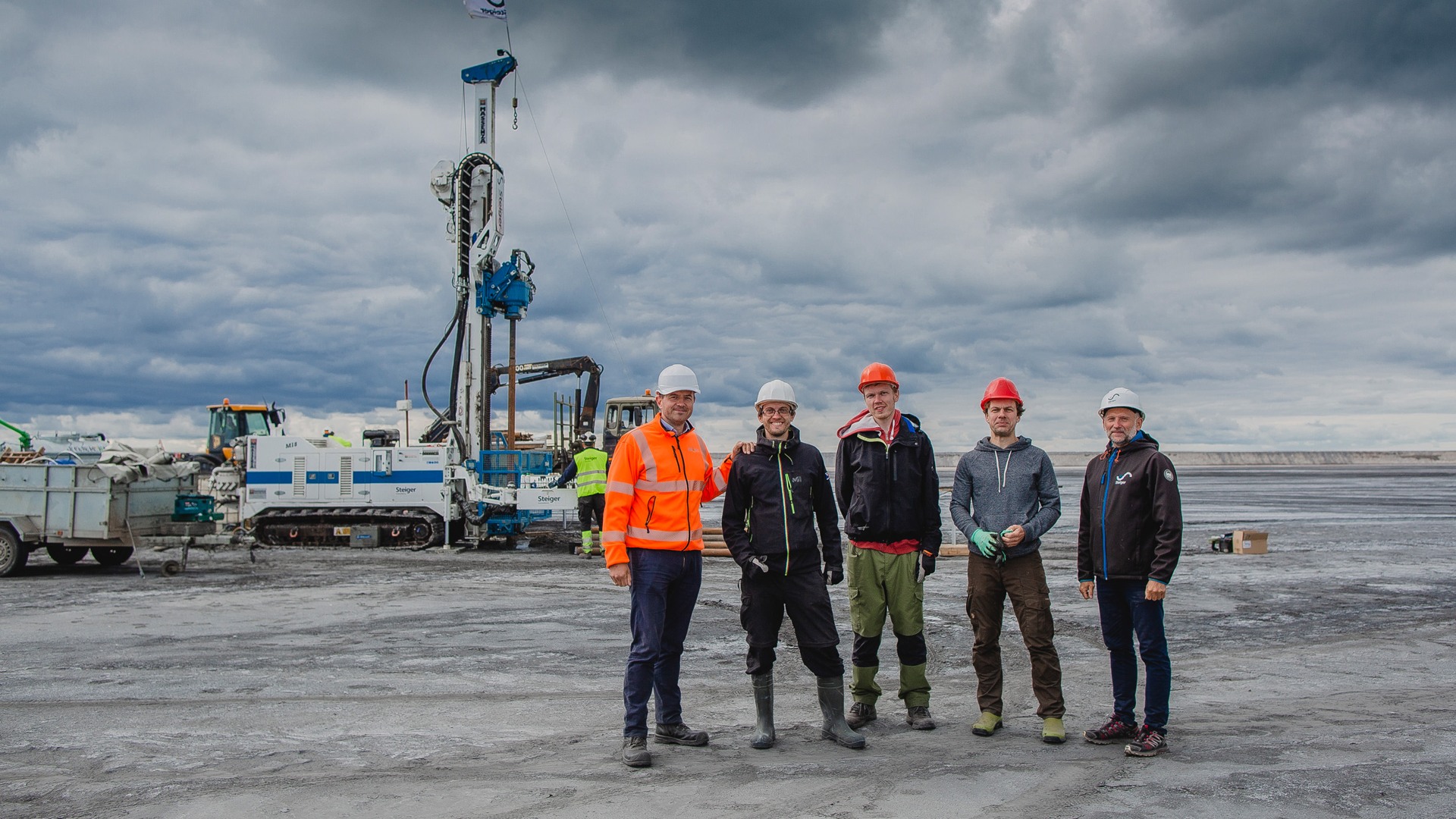
Ragn-Sells’ way of solving the oil shale ash quest in Estonia
While very few have ever even heard of oil shale, it is the number one energy source in Estonia. The country is mining 15 million tons of this brown rock per year and is left with 7 million tons of ash annually after burning it for obtaining energy. Less than a year after the Oil Shale Ash project started, the team has already filed two patent applications on how oil shale ash can be upcycled, instead of piling it as waste.
28 Jan 2021Hussain Azeez Mohamed studied environmental engineering and sustainable infrastructure at KTH when he came in touch with Ragn-Sells in 2017. Ragn-Sells knew that only 3% of the left-over ash from the oil shale industry was being used. The rest was just deposited in large mountains and wide fields and Ragn-Sells wanted to find a solution to the problem. Azeez’ task together with a fellow student was to characterize the material, figure out how toxic it was and do some simple experiments to see if some kind of industrial product could be synthesized from it. In their thesis they managed to identify a few different application areas where it could be used.
- Half a year later Ragn-Sells contacted me, asked if I was still in Stockholm and if I wanted to continue to work on this project for real. It turned out to be a dream job, very exciting and challenging at the same time, and a bit scary since it’s just been researched and not practically realised yet, says Azeez who now works as a materials development engineer at Ragn-Sells.
Motivation is key
The tests showed that calcium could be extracted from the oil shale ash, and carbon dioxide was then injected into the calcium solution. This should in theory produce calcium carbonite. The final material is called precipitated calcium carbonite, which is used in the paper and plastic industry. They now knew what they wanted to do and needed help to take the project forward.
- It’s a perfect project for Ragn-Sells, it speaks to the company and the long-term view of the project fits our strategy. It’s not just a solution for today, but also for the coming decades, says Alar Saluste, project manager at Ragn-Sells OSA Service.
Together with the Chairman of the Board of Ragn-Sells Estonia, Rain Vääna, Alar Saluste has built up an impressive network of collaborators in Estonia. The two biggest universities in the country, Tallinn Technical University (TalTech) and the University of Tartu, are involved in the project as well as Eesti Energia (Enefit) – the world’s biggest oil shale energy production company and Estonia’s largest company. Also, a number of consultants handling life cycle analysis market studies and external funding have joined the project.
- One of the reasons why it went so well was that we had very motivated resources. The universities we cooperated with really believed in the project and made it a priority. It was crucial that everyone involved saw the value of the project, says Alar Saluste.
Drilled ash samples.
Piles from the past
As an environmental company, Ragn-Sells must think of the carbon footprint. One of the filed patents need chemicals and the other one doesn’t, but the chemicals needed can be found in Estonia and doesn’t need to be imported. Estonia is geographically close to markets like Sweden and Finland which produce large amounts of paper, an industry which can buy the end product. A number of locations in Estonia suitable for a future plant have been identified. The areas have been hosting large production sites for decades and is growing tired of environmental issues also directly effecting their living environment.
- In the future we hope that Estonia will use more sustainable energy resources. Until then we have a very clear vision, to make the power produced from oil shale 100% waste free by using the oil shale ash to generate and recover resources that can be used in other production processes. Further on we can start using the ash that already has been deposited. Estonia began to use oil shale already before the Soviet times, so the piles of deposited ash are huge reaching nearly 600 million tons - the same size as the island of the Maldives, says Alar Saluste.
This amount of raw material will secure production for decades. Actually it would take about 450 years to get rid of the ash at the production rate planned for the first production plant. When looking at the longer vision of the overall project, this is just the first phase. The second phase envisioned from the year 2035 onwards, would reach a production rate of 15 million tonnes of ash taken from the mining waste heaps. Whereas the demand for captured CO2 would be corresponding to approximately 6,000,000 tonnes.
The calcium carbonate produced in the process, would totally replace mining from limestone quarries. Also, as CO2 must first be taken out from limestone by producing burnt lime, CO2 savings would reach a total of 6,000,000 tonnes.
Thinking forward
The team is confident that the applications for the two patens will be successful and are continuing to bring the project further to the next milestone in the meantime. They have a detailed time schedule until end of 2024, and if everything goes as planned the production could start in 2025.
- The important thing is that we learn, and that we build a lot of collaborations with industries, universities and other stakeholders. We are looking forward and thinking forward. There are exciting times for a company like Ragn-Sells, says Azeez Mohamed.
- There are a lot of challenges in this project and we don’t have all the answers yet. But this is not frightening, it is exciting and a part of being an innovative company in the forefront, concludes Alar Saluste.